Zugmessung aller einzelnen Nutzen
Beim Längsschneiden hat die Zugmessung von einzelnen Materialnutzen bislang hauptsächlich bei Primär-Rollenschneidern Einzug gehalten. Bei Maschinen dieser Grösse ist ausreichend Platz für mehrere einzelne Messwalzen vorhanden. Bei den kompakteren Maschinen (bis zwei Meter Arbeitsbreite) liegt der Fokus auf dem Einsatz von Wickel- und Friktionswickelwellen, um den Materialzug aller Nutzen möglichst gleichmässig zu halten. Bei diesem Verfahren bleiben jedoch die einzelnen Materialzüge unbekannt und können stark variieren. FMS bietet mit dem FMS-segFORCE® ein völlig neues Konzept. Eine Messwalze mit mehreren, unabhängigen Kraftaufnehmern zur Zugmessung in jedem einzelnen Nutzen.
Kleinste Abweichungen schnell erkennen und deren Ursache beheben
Stellen wir uns den idealen Prozess vor, würde unter gleichen Rahmenbedingungen der Schneidprozess über Wochen und Monate stabil laufen und konstant hohe Qualität hervorbringen. Die Realität sieht jedoch anders aus. Bereits beim angelieferten Material können grosse Abweichungen in der Konsistenz und den Eigenschaften der einzelnen Mutterrollen auftreten. Dies sind zum Beispiel: Streuungen bei der Materialdicke, der Dehnbarkeit, der Wickelqualität oder unterschiedliche Umwelteinflüsse auf die Ausgangsrolle. Hinzu kommen anlagenspezifische Einflüsse wie Komponentenverschleiss und thermische Einflüsse und die daraus resultierenden Unregelmässigkeiten im Verarbeitungsprozess. Die genannten Ursachen und ihre Auswirkungen sind nicht immer leicht zu identifizieren und zu beseitigen. Hersteller und Maschinenbauer im verarbeitenden Gewerbe bieten sich mit der neuen Lösung nun die Möglichkeit, den Bahnzug von einzelnen, geschnittenen Streifen präzise zu messen. Gerade bei sehr dünnen und dehnbaren Materialien und in kompakten Anlagen stellt diese Aufgabe höchste Anforderungen an die eingesetzte Technologie.
Unstetige Materialeigenschaften, variierende Prozessparameter
Schon geringe Schwankungen der Materialqualität und bei den Prozessparametern können negative Einflüsse auf die Wickelqualität haben. So können typische Fehlerbilder wie teleskopierende Wickel durch zu lose Wicklungen oder beschädigte Wickel durch zu feste Wicklungen an einzelnen Nutzen oder ganzen Nutzen-Stapeln vermieden werden. Ebenso ausschlaggebend für eine konstant hohe Wickelqualität ist der Zustand der Friktionswellen. Viele mechanische Parameter, wie Reibwerte, optimale Funktion der Friktionsringe, Zustand der Wälzlager, etc., müssen ideal abgestimmt sein, können aber nicht direkt überwacht werden. Übliche Verschmutzungen durch Staub, etc. haben hier jedoch einen negativen Einfluss, so dass konstante Qualitätsanforderungen nach einiger Zeit nicht mehr erfüllen werden. Schleichende Fehlerbilder in der Produktion werden nicht erkannt. Die Zugmessung von einzelnen Materialnutzen hilft Unterschiede zwischen den geschnittenen Streifen rechtzeitig zu erkennen. Mit der FMS-segFORCE Messwalze lassen sich solche Fehler bereits bei der Entstehung erkennen. Der Materialzug an jedem einzelnen Nutzen wird gemessen und der laufende Prozess kann besser kontrolliert und optimiert werden. Produktionsausschuss wird reduziert und Reklamationen werden vermieden. Es werden keine fehlerhaften Chargen mehr an Kunden ausgeliefert.
Aufbau der Messwalze
Die Messwalze des FMS-segFORCE besteht aus einer starren Achse, auf der die einzelnen Segmente verschiebbar angeordnet sind. Die sichere Arretierung der Segmente erfolgt pneumatisch über einen zentralen Anschluss in einem der beiden Seitenteile. Die Segmente selbst beinhalten den eigentlichen, nicht drehenden Kraftaufnehmer, einen kompakten Messverstärker und die Lagerung im Walzenmantel. Die Spannungsversorgung und Signalführung der Segmente erfolgen kabellos über die starre Achse. Eine gut geschützte, automatische Verbindung der elektrischen Kontakte vereinfacht die schnelle axiale Positionierung der Kraftaufnehmer für den jeweiligen Anwendungsfall. Für solch eine Neupositionierung muss kein einziges Kabel gelöst oder neu verbunden werden. Die Anbindung der Messwalze an den Maschinenrahmen erfolgt beidseitig über funktionale Seitenteile ähnlich eines Stehlagergehäuses. In diesen befinden sich zudem Teile der Elektronik. Gut geschützt vor Schmutz und Umwelteinflüssen. An einem der Gehäuse wird die Spannungsversorgung 24 VDC, sowie der erforderliche Druckluftanschluss angeschlossen. Zur Datenübertragung steht eine RJ45 Buchse zur Verfügung, an der die Signale abgegriffen und entweder über einen PC angezeigt, oder an die SPS weitergeleitet werden können. Anzahl, Breite, wie auch axiale Position der einzelnen Segmente lassen sich individuell auf die Maschine, sowie die Prozessanforderungen anpassen. Eine breite Abdeckung von unterschiedlichen Material- und Schnittbreiten erfolgt ganz einfach durch die richtige Zuordnung von Segmentbreiten und -abständen.
Anzeige und Datenauswertung
FMS bietet hier zwei unterschiedliche Lösungen. Mit dem PROFINET Protokoll steht eine universell einsetzbare Ethernet Schnittstelle zur Verfügung. Damit lassen sich die gesamten Messdaten in Echtzeit an die SPS übertragen. Die Ist-Wert-Anzeige, sowie die Ausgabe von Warnmeldungen bzw. Fehlerzuständen können so komplett und vollintegriert über die Maschinensteuerung erfolgen.
Eine eigene FMS-Software bietet darüber hinaus komfortable Möglichkeiten der Bedienung und Konfiguration über einen Standard-PC. Über die FMS-Software können die Kraftaufnehmer sowie die Anzeige konfiguriert werden. Eine übersichtliche Darstellung informiert den Bediener zu jeder Zeit über den Status des Messsystems.
Bildergalerie
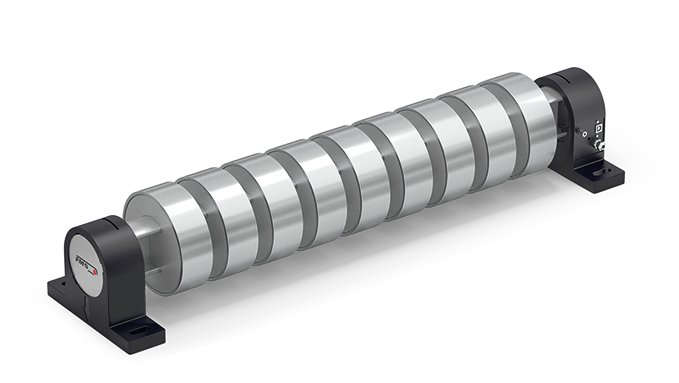
Deutlich sind die einzelnen Segmente auf der Achse zu erkennen. Jedes einzelne Segment beinhaltet einen vollwertigen Kraftaufnehmer, welcher einzeln ausgewertet wird.
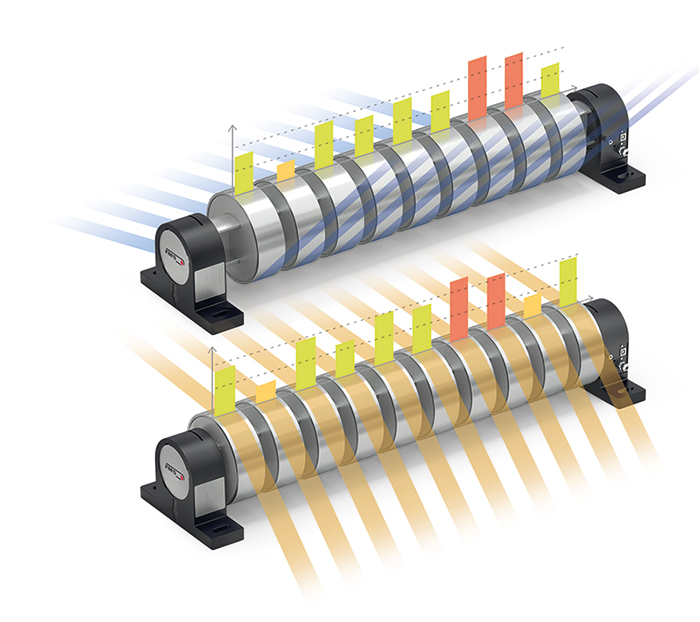
Schema zweier Messwalzen im Rollenschneider. Gut zu erkennen ist der Versatz der einzelnen Segmente von der einen zur anderen Messwalze. Minimale Zugunterschiede zwischen den einzelnen Nutzen werden schnell sichtbar. Durch die ausgeklügelte Konstruktion lassen sich alle Arten von Umschlingungswinkeln abdecken. Durch flexible Segmentbreiten und frei einstellbare Abstände zwischen den Segmenten ist es möglich, die Messwalzen für unterschiedlichste Nutzenbreiten zu konfigurieren
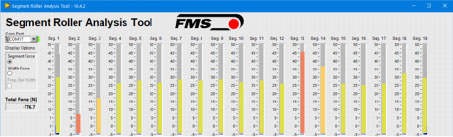
Ansicht der einzelnen Zugwerte pro Segment. Deutlich sichtbar sind die hervorstechenden Werte der Kanäle 2 und 13. Auffällige Zugwerte deuten zum Beispiel auf Verschleiss oder erhöhte Temperatur einzelner Friktionselemente hin. Hervorgerufen beispielsweise durch Verschmutzung.
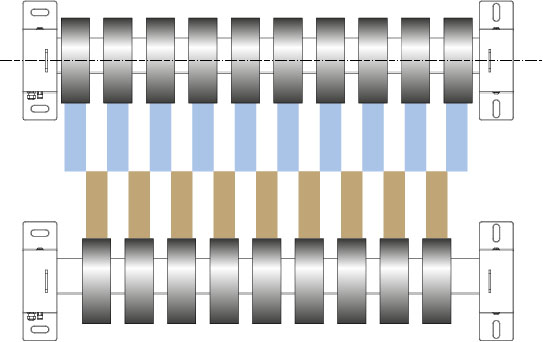
Schnitt 1: 1 Segment pro Abschnitt
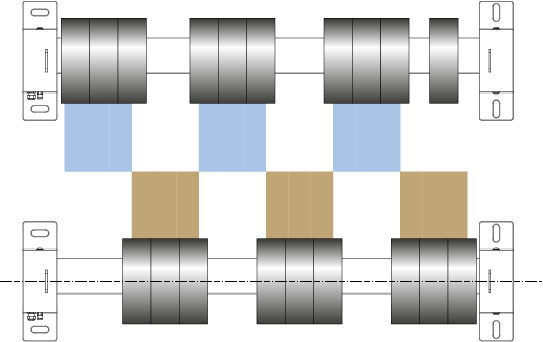
Schnitt 3: 3 Segmente pro Abschnitt
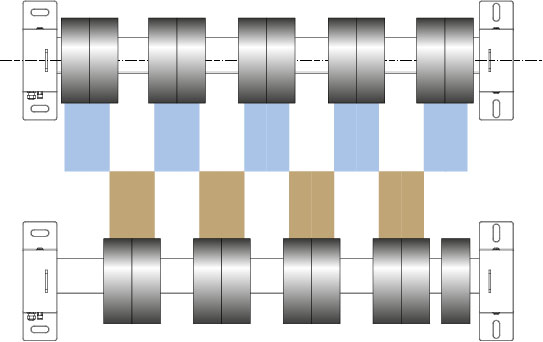
Schnitt 2: 2 Segmente pro Abschnitt
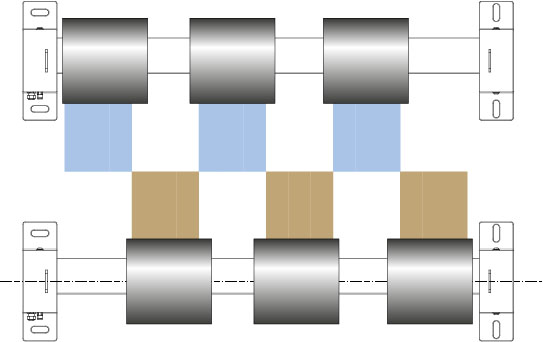
Schnitt 4: breitere Segmente
Die Illustrationen zeigen Beispiele für die Anpassungsmöglichkeiten zwischen Schnittbreite und Segmentbreite. Es wird jeweils aus identischem Ausgangsmaterial eine unterschiedliche Anzahl an Streifen geschnitten. Die Anzahl und Breite der Segmente, die am besten und effizientesten einsetzbar ist, wird ebenfalls durch die gewünschten Schnittbreiten bestimmt.