FAQ - Frequently Asked Questions
Here you will find the answers to your most frequently asked questions.
Web Tension
How is web tension measured?
The web tension is measured indirectly via an idler roller over which the web is guided. The tension of the web creates a load on the roller. This load can be measured by two force sensors (load cells) on each side of the idler roller.
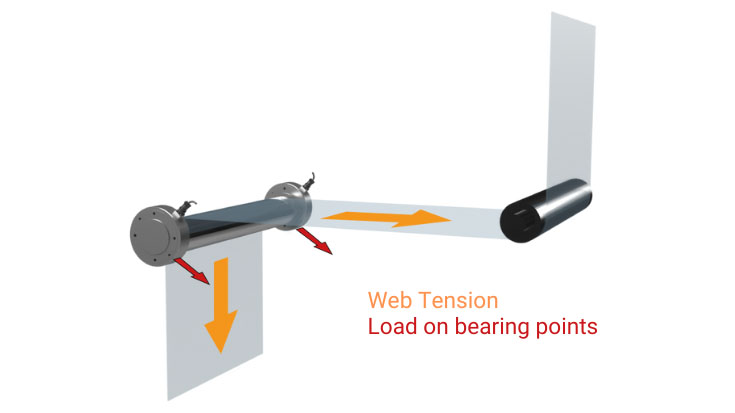
What is the unit of web tension?
Web tension is nothing other than a tensile force. The SI unit for force is Newton N (metric), or Pound-force lbf (imperial). A typical unit, independent of the material width is N/m or lbf/in.
What is the torque of web tension?
Web tension and torque are linked by a mathematical formula. Torque = web tension x radius of a roll. If I want to keep the web tension constant, simple rules apply: If the diameter of the rewinder increases, I need increasing torque on the rewind shaft; if the diameter of the unwinder decreases, the torque of the unwind shaft decreases.
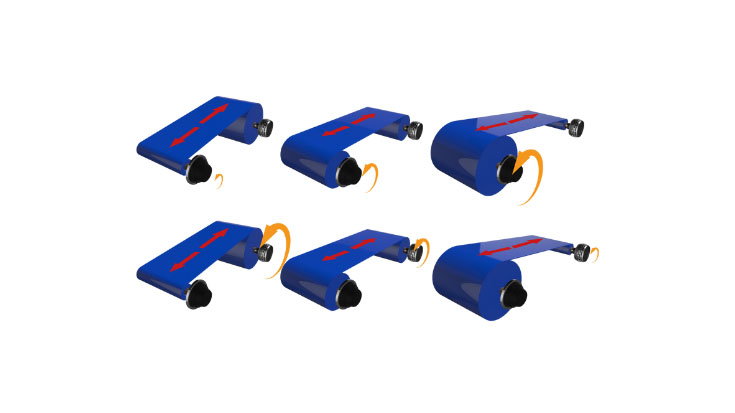
Force Sensors
What is a force sensor?
Force sensors are used to measure compression, force, strain and load. Many have internal strain gauges bonded to the metal structure which react to even the smallest deformation causing a change in resistance and giving feedback on these results. Force sensor is an alternative term, depending on the design and application they may also be called load cell, force transducer or force measuring bearing.
Where are force sensors used?
One of the most common uses is for tension control applications. Web type material is fed over an idler roller. Force sensors on each end of this roller detect the force that acts on the roller generated by the material tension. The feedback signal from the force sensors is processed and delivers a direct indication of the strain or tension in the material in Newtons, kilograms, grams or pounds. Applications for wire tension control apply a pulley/sheave and a single force sensor instead of the roller with two force sensors.
What is the difference between dead shaft and live rollers?
Dead shaft rollers are usually made of two separate parts. The non-rotating axis and the roller sleeve are connected via bearings. This allows the sleeve to rotate around the axis. In contrast, live shaft rollers are made from one piece. Bearings sit in each force sensor on either end of the roller. Dedicated types of force sensors are available for both types of rollers.
What is the nominal force of a force sensor / load cell?
The required nominal force FNom of a force sensor must be calculated individually per application. It determines the maximum force that a sensor can measure. Higher loads on the force sensors by web tension and the weight of the idler roller result in higher FNom. For applications where you use two force sensors on each end of an idler roller (typically for web tension measurement) the maximum load is divided by two, as the force is distributed evenly to the left and right. For FMS force sensors, the FNom is always specified in direction of the Red Point as this marking defines the measuring direction with positive sensor signal. The following information is essential for the calculation of FNom:
- entry and exit angle of the web (wrap angle) in relation to the horizontal ((to obtain a reference to the weight force)
- web tension (typically min. and max. values)
- weight of the idler roller.
For easy and quick estimation of the required FNom, FMS offers a free online tool – the FMS Calculator
How does the nominal force affect the measuring range of a force sensor / load cell?
Many specifications of a force sensor refer to its nominal force FNom. This also applies to the measuring range. The measuring range is made up of the upper and lower values. The upper value is the nominal force, the lower value is calculated from the quotient of FNom. Typical specifications for the measuring range of FMS force sensors are 1:30 or 1:100. The following example shows the calculation of a LMGZ-series sensor with a FNom of 1´000 N. The measuring range always refers to the entire measuring range. In case of web tension measurement with two force sensors on an idler roller, the measuring range refers the mean value of both force sensors.
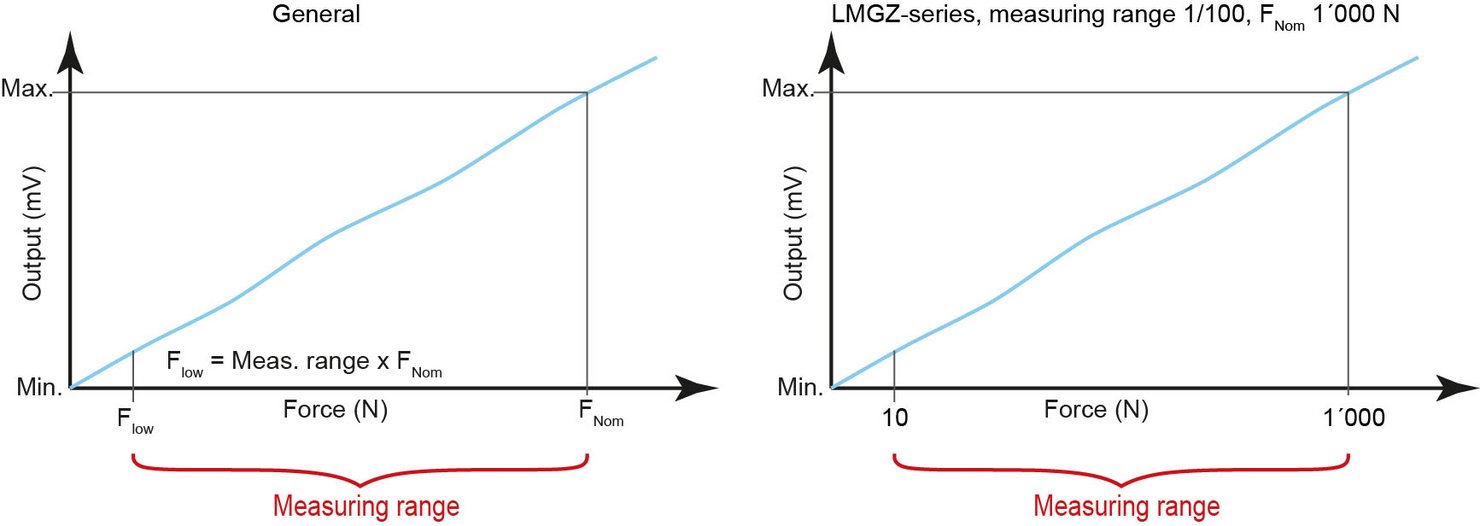
What is the accuracy class of an FMS force sensor / load cell?
FMS defines the accuracy as a function of the nominal force FNom of the respective force sensor and refer to this as the accuracy class. The accuracy class is made is made up of linearity error, hysteresis, and total error. All three influencing factors are verified during the final inspection of a force sensor before shipping. The accuracy class applies in the entire measuring range of the force sensor.
FMS-Calculator
What is FMS-Calculator?
FMS-Calculator is a browser-based program for sizing and selection of FMS force sensors.
Are there restrictions in the FMS-Calculator?
There are many factors you need to consider during the design phase. In addition to supposedly fixed specifications such as environmental influences and installation space, there are also other, often not yet defined boundary conditions that may change in the course of a project. To take these into account, we recommend that you discuss your designs with us. Our specialists can help you even if the application specifications may not lead to a clear result.
Which languages are supported by FMS-Calculator?
FMS-Calculator supports German and English. You can select the language as well as your preferred units in the settings.
Can I save calculations in the FMS-Calculator?
Yes, you can save any calculation. Create a project or add your calculation to an existing project and you can access it again at any time.
Can I exchange calculations with other users?
Projects and corresponding calculations can be shared with other Calculator users. On the project administration mask, you can add the email-address of the users you want to add to the project. Feel free to also add your FMS sales representative to get support with your calculation.
How can I size double-range force measuring of the LMGZD series?
Enter the maximum AND minimum material tension. Go to the Optimization step and select a dual-range force sensor of the LMGZD series. Select the size and nominal force and check in the force diagram (on theleft) whether the force sensor is suitable or not.
How are the results displayed in the FMS-Calculator?
After successful sizing completion, you can output the result as a file in a pdf format. The file is ideal for your internal documentation or further optimization.
What are the system requirements for the FMS-Calculator?
A computer with web browser and internet access.
Measuring Amplifiers
What are the advantages of ethernet communication over power outputs on a measuring amplifier?
The resolution of sensitive force sensors and amplifiers can be used much better using a 16 bit word instead an analogue signal (with a measuring range of 1:50 the signal is as small as 20 mV at lowest measurable point). Wiring of machines can be reduced a lot, and especially modular machines are much easier to connect from module to module.
What’s the difference between analogue and digital measuring amplifiers?
Analogue amplifiers use many more components that are temperature dependent, the worst being the potentiometers to adjust offset and gain. Signal filtering depends on capacitors that will lose their capacity over time. In digital amplifiers all parameters are stored reproducibly in a memory facilitating a replacement without recalibration.
Segmented Tension Roller
What is the FMS-segFORCE?
The FMS-segFORCE segmented tension roller is a new, advanced device designed to monitor web tension more accurately then conventional tension monitoring. It features multiple independent force sensors along the roller to provide detailed tension profiles.
What is the difference between conventional tension monitoring vs the FMS-segFORCE?
A roller with a set of standard loadcell can only measure the average tension across the width. Using a double-channel amplifier one can detect higher or lower tension on left or right side. With the FMS-segFORCE one gets a tension profile with up to 50 measuring points across the width of the web material. The resolution of the profile can be set by selecting appropriate segment width and quantity.
Where is the FMS-segFORCE applied?
One main application is in the quality control of web material. The tension profile can be used to identify defective material and exclude it from further processing steps. The causes can be determined and corrected before valuable machine hours are lost. The tension of the individual slit strips can also be measured in secondary slitter / rewinders. Deviations are directly indicated, and suitable countermeasures can be taken.
What kind of defects or properties can an FMS-segFORCE detect?
The FMS-segFORCE has been applied in a wide range of applications and industries. From film extrusion, coating to slitting, from battery foils to sandpaper production. The following list is only an excerpt of possibilities.
- Loose edges
- Baggy web
- Single-sided tension
- Not properly aligned idler rollers
- Uneven coating thickness
- Defective differential shafts
- Out of round parent roll
- Gauge deviations
What is a tension profile created with the FMS-segFORCE?
The FMS-segFORCE is a tension measuring roller with up to 50 independent force sensors across the entire roller. The sensors can be placed directly next to each other. Each of them generates a tension reading for the respective part of the web. If you take all these values together and arrange them according to time, you obtain a tensile profile. A tensile profile can be used to make direct statements about the quality of the web. Defects such as loose edges or droopy web are easy to recognize.
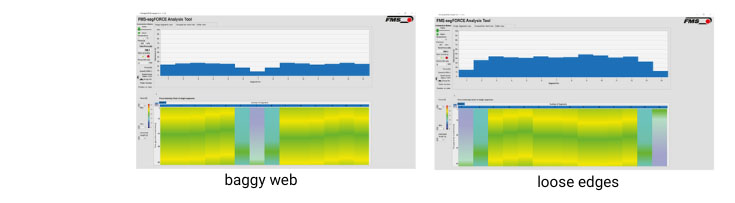
Can the FMS-segFORCE cut down costs?
Yes, the FMS-segFORCE can help you to detect scrap production in a very early stage. Before you waste valuable operator and machining hours, the FMS-segFORCE detects faulty material and allows you the react in time. Change material, safe time and costs.
Web Guiding Solutions
What is a web guide?
Web guides are typically used where web type material is processes from roll-to-roll. These devices control the lateral alignment of the web. Any misalignment is detected with material sensors and directly leads to a correction by the actuator. In general, three components are required for all types of web guides:
- Material sensor – Depending on the web material, ultrasonic or optical sensors are used to detect the edge of the web. This signal with the actual position of the web is then sent to the
- Web guiding controller – Controls the closed-loop functionality of the entire system. It comes with display and operating options. If the deviation between the actual and reference values is too high, the controller will send a signal to the actuator to correct the position of the web immediately.
- Actuator - Mechanical assembly that "moves" the material web sideways. Due to the different installation situations, there are many types of actuators.
The different types of web guiding systems are also named according to the type and characteristics of the actuators. Here are the two most important ones:
Linear actuators – Used at the beginning or the end of machines. An unwinding station holds the parent roll and feeds the web into the process. To adjust the alignment of the web, a linear actuator is used to push the entire (unwinding) assembly back an forth.
Steering frame – Used for intermediate web guiding inside the machine, mainly prior to an important process step. The web path with four times 90° wrap angle of the material is typical for steering frame web guides. This avoids shear stress on the material web.
What is the web handling principal or normal entry rule?
If a web is in traction with a roller (idler or driven) it seeks to align itself perpendicular to the roller. That means that in a complex machine with many rollers, the precise parallel alignment of the rollers is essential for its functionality. Nevertheless, the web guiding system can rarely be avoided.
Telemetry Systems
What are telemetry systems?
Many types of stranding machines are used in the wire & cable industry. The special design often does not allow the use of cables for the transmission of signals and measurement data. Instead, systems that use radio for data transmission are used. FMS has multiple systems in this industry. Over the last few decades, FMS has developed several such systems for different types of machines and applications. All of them use wireless signal transmission and are summarized under the umbrella term telemetry systems.
What is the RTM X42 Telemetry System?
It is a retrofittable system for strand tension monitoring and tension control in stranding machines. Up to 42 force sensors on the layplate, shortly upstream the stranding point, measure the tension of all individual strands. The readings are transmitted wirelessly to the operator’s station and displayed graphically.
- Objective tension reading support the operators
- Helps to get equal tension on all strands
- Increased product quality
For further automation of your production the systems can be extended to a full closed-loop tension control system. Friction type brakes can be equipped with brake actuators on each cradle. They automatically readjust the brake tension of each spool depending on the preset reference tension of the respective strand.
- Uninterrupted production, w/o downtimes for manual readjustment of brakes
- Absolute safe and repeatable processes für further relief of operators