Up to 50 measuring points in a single roller
One of the most important requirements in coating lines is the tension-stable feeding of the different substrates into the individual manufacturing processes. A corresponding web tension control system usually consists of FMS force measuring bearings on both sides of an idler roller, which form the mean value over the entire tension across the web width. However, extremely sensitive materials or processes with higher requirements (process data acquisition, digital roller protocol, Industry 4.0) require a higher resolution of these tension values over the width of the material web and thus several measuring points within the respective material web width. FMS offers a novel concept here with the FMS-segFORCE®. A measuring roller with several independent force sensors.
Detecting transients and eliminating causes
The example of curtain coating illustrates the sensitivity of the various coating processes. All plant components and parameters must be ideally matched to one another to achieve the best possible coating results on different substrates in a wide variety of material widths. Transients, e.g., from environmental influences, such as temperature-dependent changes in substrate behavior, have a major influence on the required manufacturing quality. Mapping the tension distribution over the entire width of the material web provides new insights for process optimization.
Uneven tension distribution across the web width
If a high quality standard is to be ensured throughout the entire production process, the demands on the raw material (parent roll) are already extremely high. Due to different pre-processes, transport routes or storage, this raw material may already have experienced a wide variety of influences. Different winding qualities, large temperature fluctuations or mechanical deformations are an issue here. For example, overstretched material edges or material areas deformed by impacts cannot be detected with conventional measuring technology. For example, overstretched material edges or material areas deformed by impacts cannot be detected with conventional measuring technology.
Tension profile for simple fault detection
With up to 50 measuring points along a measuring roller, the FMS-segFORCE offers the possibility to subdivide the entire web tension into individual segments and to display the material tension of the individual segments in a so-called tension profile. For example, irregularities in the quality of the raw material or problems in the manufacturing process can be identified quickly and easily. Process- or material related defects and faults can be easily identified over time. This information is used for further process analysis and optimization.
Measuring roller design
The FMS-segFORCE measuring roller consists of a rigid shaft on which the individual movable segments are arranged. The segments are securely locked in place pneumatically via a central connection in one of the two brackets. The segments themselves contain the actual force sensor, a compact measuring amplifier and the bearing in the roller shell. The segments are supplied with power, and signals are routed wirelessly via the rigid shaft. A well-protected, automatic connection of the electrical contacts simplifies the force sensors' quick axial positioning for the respective application. Not a single cable needs to be disconnected or reconnected for repositioning of the measuring segments. The measuring roller is connected to the machine frame on both sides via functional brackets similar to a pillow block. These also contain parts of the electronics, well protected from dirt and environmental influences. The 24 VDC power supply and the required compressed air connection are connected to one of the housings. An RJ45 socket is available for data transfer. The signals can be picked up and either visualized via a PC or forwarded to the PLC.
Display and data analysis
FMS offers two different solutions. The PROFINET protocol provides a universally applicable Ethernet interface. It can be used to transmit all measured data in real time to the PLC. Thus, the machine control can be used for displaying actual values and outputting warnings or fault states in a fully integrated manner. In addition, a separate FMS software offers convenient configuration options via a standard PC. The force sensors and the display can be configured via the FMS software. A well-arranged display informs the operator at any time about the status of the measuring system.
Image gallery
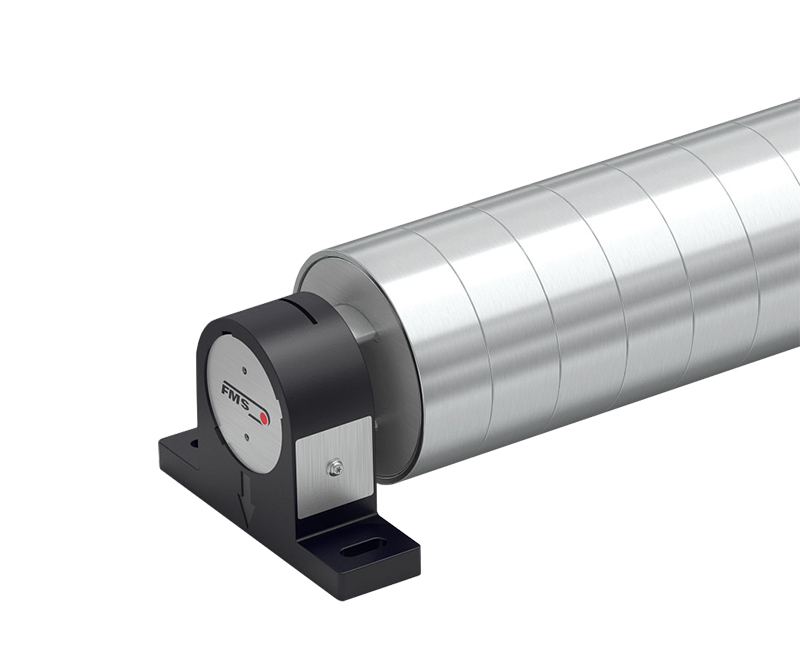
The lined-up individual segments can be seen clearly on the shaft. Each individual segment contains a fully-fledged force sensor with preamplifier. Due to the homogeneous roller surface and the small distances between the segments, there is no risk of damaging the material web surface.
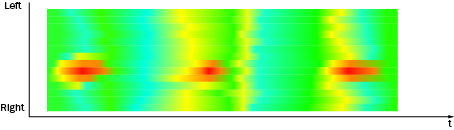
Typical defect pattern in a coating application where there is an inconsistent spray pattern, faulty nozzle or saturation issue into the substrate. This fault cannot be detected using a conventional measuring roller.
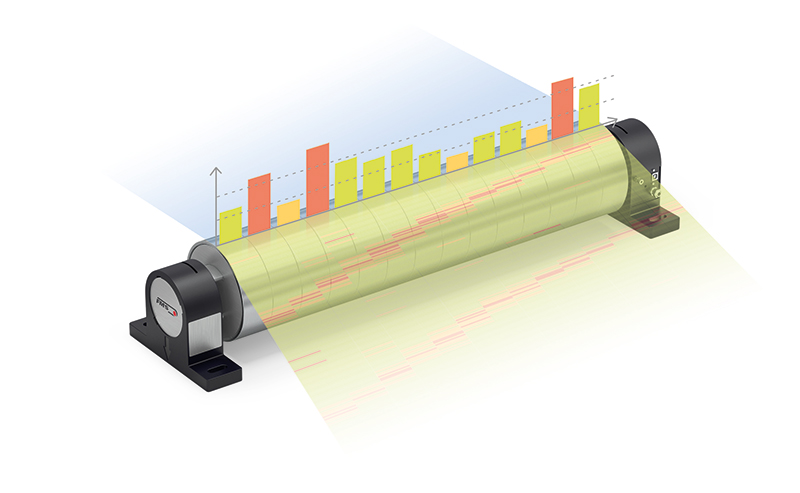
Fully equipped segment measuring roller on pillow blocks for universal mounting on the machine frame. All that is required is a 24 (18 to 38) VDC power supply and a compressed air connection. The data is transferred via an RJ45 socket.
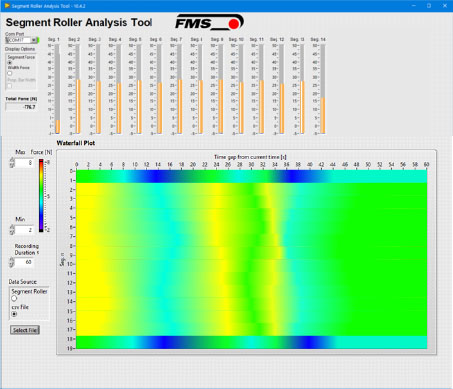
Typical defect pattern for loose, overstretched edges. Top: Measured values of the individual segments. Bottom: Waterfall plot. This fault cause cannot be detected using a conventional measuring roller.
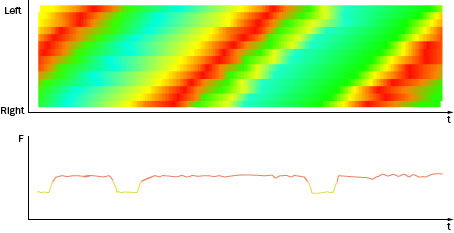
Tension profile (top) with measurement data from 14 individual segments vs. conventional tension measurement with "mean value" (bottom)
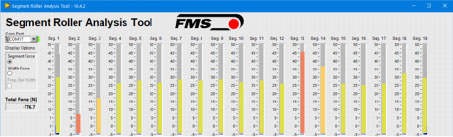
Tension values of the individual channels.
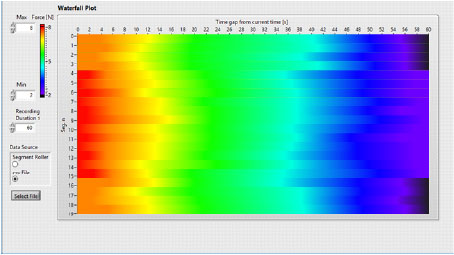
Tension profile with 20 segments over time (waterfall plot) - the decreasing tension across all channels can be clearly seen.